Anku Guha
(Graduate Student, TIFR Hyderabad)
By the middle of this century, it is estimated that the world’s population shall touch the 9.8 billion mark. This will result in increased requirements of both energy and food. For energy, we are mostly dependent on fossil fuels such as coal, oil and natural gases, the reserves of which are limited. The excessive use of fossil fuels emits huge amounts of carbon dioxide – a greenhouse gas that contributes to global warming.
To minimise the dependency on energy sources that emit carbon dioxide, scientists have concentrated their efforts on developing the renewable sources of energy like solar energy, hydrogen fuel cell etc. Hydrogen can be renewably produced by electrolysis of water, following which it can undergo combustion and electrolysis in a fuel cell to provide energy. This is one of the most promising ways to obtain a carbon dioxide free energy source that leaves only water as a benign byproduct. However, hydrogen is a very flammable gas. The storage and transport of hydrogen gas bottlenecks the commercialization of hydrogen fuel cell technology. This issue can be solved by storing hydrogen in the form of ammonia. Ammonia contains 17.6% hydrogen by weight. Additionally, the energy density by volume of ammonia is double that of liquid hydrogen. The ease with which hydrogen can be extracted from ammonia presents commercially viable opportunities for the storage and transport of an otherwise flammable fuel.
How does one obtain sufficient reserves of ammonia? In 1909, Fritz Haber discovered that nitrogen can be artificially converted into ammonia by reacting with hydrogen on an iron catalyst, under very high pressure (around 250 bar) and temperature (around 350oC). This process was commercialized by Carl Bosch. Till date, the Haber- Bosch process is the only commercially viable process that artificially fixes aerial nitrogen in the form of ammonia. The Haber- Bosch process uses hydrogen from steam reformation of coal and natural gas, leaving behind carbon dioxide. The additional requirements of high pressure and temperature conditions translate to more burning of fossil fuels and more carbon dioxide emissions. The Haber-Bosch process consumes about 5% of the world’s natural gases and releases 1% of all carbon dioxide emissions making it one of the dirtiest industrial processes. Hence, an environment friendly process of synthesizing ammonia is desirable.
Instead of breaking the N-N bond using thermal energy (as in the Haber-Bosch process), there also exist other alternatives, for example using an electric potential across a reactant filled solvent. This process can electro-chemically oxidise or reduce a small molecule. Electrochemical reduction of nitrogen in an aqueous electrolyte to yield ammonia could perhaps be a good alternative. But what exactly is this method? I will try to explain the experiment using the picture below as a visual tool. In this process, a two compartment H-cell (that is shaped like the letter H) is used. Different processes take place in the two compartments, which are separated by a proton exchange membrane. In the working electrode chamber, nitrogen is used as a feeding gas to introduce soluble nitrogen in the electrolyte and water is used as a proton source. By the reduction of N2 and H2O, ammonia (NH3) is produced along with hydrogen gas (H2). This hydrogen evolution reaction, in aqueous medium, is the main competing reaction for the desired electrochemical nitrogen reduction. In the other chamber, oxygen is generated by oxidation of water.
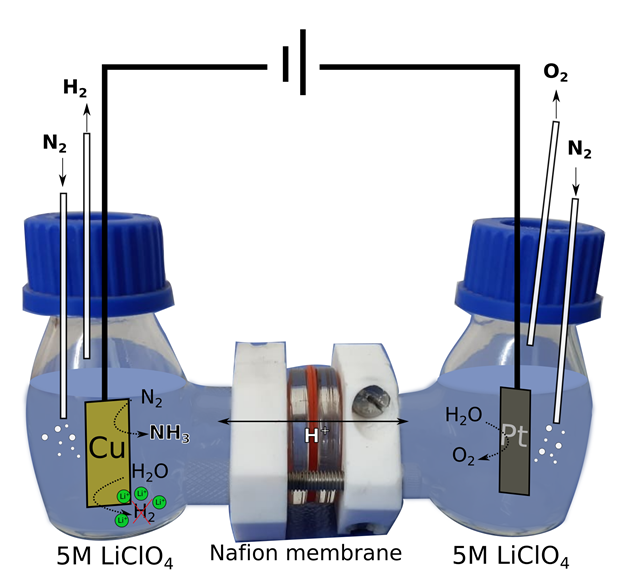
The produced ammonia mainly remains as dissolved ammonium in the electrolyte. The electrochemical reduction of nitrogen to ammonia can be performed at ambient conditions, which makes it an attractive alternative. Also, the electric potential required can be fulfilled using renewable electricity sources like wind, solar energy. However,there are certain drawbacks to this method such as, (a) nitrogen is very stable and requires very high energy to split the bond between the atoms, (b) hydrogen gas generation along with ammonia, (c) insolubility of nitrogen gas in water.
To solve these issues, one of the earliest initiatives were taken by Tsuneto and his colleagues in 1994. They used lithium perchlorate in tetrahydrofuran (a non-aqueous electrolyte) to avoid hydrogen evolution reaction and used ethanol as a proton source. They successfully achieved 57.7% energy efficiency (the ratio of energy output and energy input). One major drawback was that this process required high pressure conditions (50 atm).
Our goal was to synthesize ammonia under room temperature and pressure in an aqueous electrolyte, using aerial nitrogen. For this electrochemical nitrogen reduction, we chose copper as a model electro-catalyst. Copper also happens to be one of the cheapest metals with reasonably high concentration present in the ores. Furthermore, when copper is used, the hydrogen evolution reaction is reasonably less.
Now, the main challenges that remain are breaking the stable bond between nitrogen atoms and the solubility of nitrogen in the aqueous electrolyte. To bypass the first problem, we used concentrated aqueous lithium perchlorate as the electrolyte. Lithium ions attract nitrogen, thereby increasing the distance between two nitrogen atoms, and less potential is required to split the nitrogen molecule.
While most previous studies rely on modifying the electrocatalyst, this is the one of the first reports wherein the electrolyte undergoes modifications. A wide range of potential and variation in the concentration of lithium ions was studied to optimize the reaction. Ultimately we achieved an energy efficiency of 12.1%, at relatively low over potential (−0.6V vs. RHE) as compared to a conventional nitrogen reduction reaction (-0.35 V vs. RHE).
We performed nitrogen reduction for 19 hours at a stretch to see whether the copper catalyst could sustain the reaction while maintaining the same energy efficiency, and without any permanent modifications to the catalyst. We observed that the produced ammonia linearly increases with time and no other nitrogen containing byproducts, such as hydrazine, are detected. This confirms that our electrochemical nitrogen reduction process is highly selective and durable.
Though a 12.1% energy efficiency of nitrogen reduction in ambient condition is achieved, it is still far from commercialization. Also, a detailed mechanism of electrochemical ammonia synthesis remains to be known. Altogether, the concept of electrochemical ammonia synthesis using a supporting electrolyte like lithium perchlorate provides helpful insights for designing reactions in the near future, ones that can speed up the synthesis of ammonia in ambient temperature and pressure.
Featured image: Pixabay
Read this article in Telugu and Bengali.